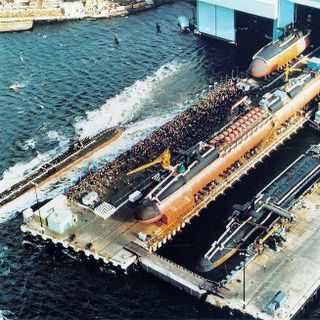
General Dynamics Electric Boat (Source: US Navy Photo)
The last 688, a 688i variant, SSN 773 the USS Cheyenne was delivered to the Navy in September 1996 by NNS. Since then EB has delivered three SSN 21 Seawolf class submarines, was the lead designer of the new Virginia class submarine and delivered the SSN 774 USS Virginia in October of 2004. Newport News has not built another submarine since 1996 until the recent launch of the USS Texas SSN 775 in April of 2005. Newport News Shipbuilding also produces the best Aircraft Carriers in the world, the Nimitz class, of which nine have been built and one is currently in construction.
Therefore, who builds a better submarine General Dynamics Electric Boat or Northrop Grumman Newport News Shipbuilding? I was qualified on and rode two different boats, one built by NNS in 1965 and another built by EB in 1985. Not a fair comparison two different classes with 20 years difference in technology and design. And as I indicated before I was once a EB yardbird, so there is a built in bias here, fair warning in where I’m going with this.
Newport News has always built a quality submarine. The USS San Francisco SSN 711 built by NNS ran into a seamount at a full bell crushing it bow in January. The San Fran may not have survived if not for the quality of its construction and professionalism of the crew. But if being the “Best” means also staying on budget and delivering when contracted to then Newport News get a losing grade. NNS will not deliver the USS Texas to the Navy until May 2006 almost a year after the initial projected delivery date. Newport News Shipyard’s construction of the Texas is also an estimated 24 percent over projected cost.
Lead units are usually problematic and NNS will have had a nearly 10 year hiatus between deliveries of its last two submarines, but the Virginia class is different. In order to maintain two active submarine construction yards, production of the 10 projected Virginia class submarines is being split between EB and NNS with whole systems produced by one or the other. For example, EB will build the ships Command and Control Systems and NNS will build the Weapons Systems. Final submarine assembly will be split between each shipyard EB has completed the USS Virginia and NNS is in the process of completing the USS Texas. This is different from the 688 contracts where each yard did the bulk of its own component fabrication and construction.
Therefore, here is my argument, its not who builds thE Best submarine but who is the better shipyard at submarine construction? Both shipyards have had their share of cost overruns and problems and in the end both build a quality submarine. However, Electric Boat has an advantage in that its only business is in the design and construction of nuclear submarines for the US Navy. Newport News Shipyard builds submarines as well, but also produces Navy surface ships and has an extensive surface ship overhaul and conversion business. Additionally Electric Boat’s Quonset Point facility is dedicated to the quality fabrication of submarine pressure hull sections. In fact, a major portion of the pressure hull sections that NNS will use in the construction of Virginia Class subs will come from Electric Boat Quonset Point. Also recently the Navy has been concerned about NNS construction delays and cost overruns has asked EB to take a more active role as the lead design yard in managing Newport News Shipyard’s Virginia class submarine construction program.
With the current reduced production rate of submarines the Navy is hard pressed to keep two shipyards building submarines efficiently. Therefore, at 1.6 billion the Virginia class submarine was to be a cost saver for the Navy and far cheaper than the 2.8 – 3.0 billion Seawolf class, but the current Virginia class subs are now costing between 2.4 -2.7 billion a copy. With the current procurement rate of one submarine a year that cost could drop to just around 2.0 billion per hull if the build rate were increased to two subs per year. A side note two new subs a year would also keep our force level at it’s current state where as the one per year rate will further reduce the size of the SSN fleet as older 688s are decommissioned.
The Navy has some tough choices. In order to keep a two competitive shipyards producing submarines it must split what a single shipyard could handle easily between two yards. However, this decision comes at the expense of higher production costs. There is no economy of scale in production and smaller regional parts suppliers can no longer be supported by the effective reduction of orders. Additionally the shipyards are forced to retain higher cost engineers and trades people in order to maintain the required instructional skill sets while reducing their work force. These highly skilled shipyard workers end up back filling functions that are below their skill level or worse doing busy work thereby further driving up production costs.
Hopefully the Navy and the two remaining submarine manufactures EB and NNS can made this joint production competition/non-competition thing work. But if not and costs drive procurement rates down like the Seawolf class, from 29 hulls down to only 3 we could some day be saying that a foreign manufacture builds the “Best” submarines in the world.
3 comments:
Great post Lubber. Very interesting and informative analysis.
That story reminds me of the "old" days, when Bath Iron Works (BIW) was cranking out FFG-7s so fast, the Navy couldn't get the crews tarined fast enough. The Todd shipyards (Seattle and somewhere in CA) were way behind schedule building the same hulls.
Also, I was pre-comm on a 963, assigned as the laision between the Ingalls Shipbuilding/SupShip guy and the ship in 79, so I got a lot of insight into the way they went together. In 84, I was Engineer on 979 and was sent to BIW for ROH. We were the first 963 BIW worked on, so it was exciting trying to tell them it was not an FFG, but even more interesting when one of the BIW crew would come and get me, to take me to some remote location on the ship and to point out bad (Ingalls) workmanship from the build). Competition...and then again BIW cranked out plenty of DD/DEs in WWII, with a reputation for making solid ships that took a lot of punishment. That pride of workmanship was still very much in the BIW culture in the 80s...
Chaotic, I've always heard BIW was one of the best yards around thanks for some "been there" style confirmaion.
I'm of the opinion EB has the same type of culture as BIW. When I was a yardbird at EB in the late 70's my lead supervisor, Len, was a third generation EB shipyard worker. If he were in the Navy he would of reminded you of one of those old salt Master Chiefs that had been to sea on the USS Constitution. Len was a toolmaker machinist knew his Sh*t. I'm sure EB still has a few Lens still working there.
Post a Comment